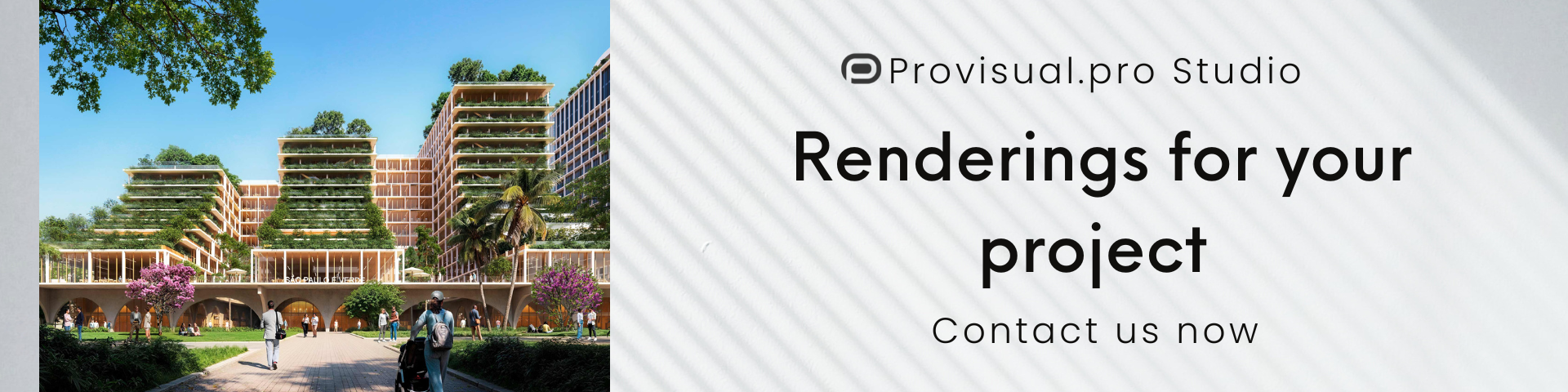
Spot welding is a process by which two pieces of metal are joined together in a permanent manner at a number of points (aka ‘spots’). This is done when an electrical current is passed through the point at which the weld is desired and the resistance creates heat, thereby melting the two points together. Frankly, after months of dealing with things like rhino and spider joints, it’s a relief to come across something where the name is so clearly indicative of the actuality.
Matthew Borgatti, a designer and fabricator, was interested in adding one of these machines to his workshop because of its capabilities for doing bent wire construction and sheet metal enclosures and it doesn’t require a great deal of shop space. Borgatti, desirous of enhancing his prototyping process, decided it was time to make one.
“I’ve used spot welders for a long time in metal shops. I was a machinist and metal fabricator for a couple of years coming out of college,” said Borgatti. “I did a lot of the metal coursework in industrial design at Rhode Island School of Design and that became my career for a while. Now that I have my own independent shop, I have for years focused on digital fabrication doing 3D printing and laser cutting to get work done and as I’m trying to increase my powers of prototyping I realized that there was some additional equipment that I could use.”
As a long-time Instructables member, Borgatti had access to a world of expertise in DIY and after going through a number of tutorials and watching a video on YouTube by a contributor known as The King of Random, he came to a decision.
“I realized that when I passed a dead microwave on the street that I had everything in my shop, plus that microwave, to build my own spot welder. I own a laser cutter, I’ve got a 3D printer to do the brackets, I used the fastenings that I had around and I made electronics with what I had in my scrap bin,” he said.
In an interview with 3Dprint.com, Borgatti detailed the process for creating his microwave spot welder:
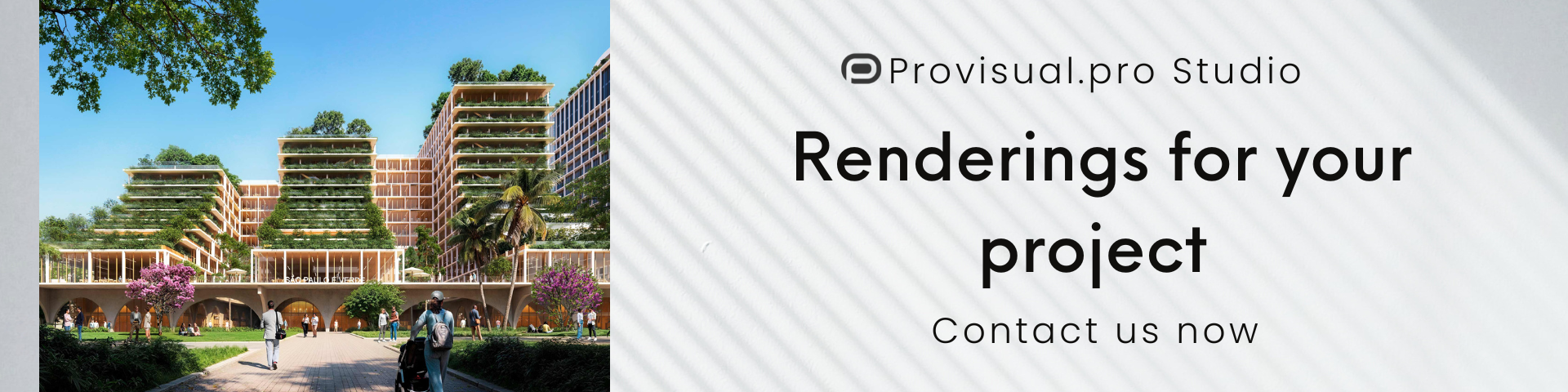
“I do a lot of SolidWorks stuff, it’s my program of choice. I started with bench tests, pulled apart the microwave, put together temporary circuits to run the transformer. Rewound it, first using a heavy gauge cable that I made by stripping thinner gauge cable and folding the copper together as a proof of concept. When that worked, I invested in heavier duty cable. I took measurements of all of the important components, figured out how I wanted it to behave, put it into SolidWorks and worked with a bunch of different iterations to try out a number of versions.”
The metal electric pieces that form the core of the creation are surrounded by laser cut parts that are fitted together with 3D printed components. The transformer, some of the wiring and spade connecters, circuitry, and the power cable were able to be salvaged from the abandoned microwave. After finalizing the designs for the laser cut parts and cutting them out of acrylic, he turned to the creation of the 3D printed components.
“I built a bunch of corner connectors out of the 3D printed PLA on my Ultimaker2. The way that I designed everything was to minimize the number of additional fasteners. So, I tapped the PLA parts, they had a high wall thickness and a heavy infill to have more meat to tap, then I tapped them with an M5 and then I also had the laser cutter actually cutting out the pilot hole for tapping,” Borgatti explained.
All told, the build took approximately four days but at the end he had a machine that could “magically” spot weld. Well, it’s not magic really, it involved changing the output of the transformer from the high voltage pulse used in a microwave magnetron. Changing the number of turns of the primary and secondary coil allowed him to tune it to produce the low voltage pulse necessary to create the heat resistance. When two materials are clamped together, the heated point welds together specifically where they touch because of the increased resistance from the tiny air gap that exists between the two different components.
He hopes to be able to use the microwave spot welder’s ability to weld sheet goods together to continue to add to his tools.
“I would like to create a CNC desktop plasma cutter that I think I’m going to lead my shop in that direction for creating holding mechanisms for stepper motors, for creating structural elements for CNC machines. I think this is a good direction for a small fabrication studio, especially because the kind of work I do through my company SuperReleaser is generally equipment design. I’ve worked, for example, CNC plotter robots that move pens around reproducing people’s handwriting and other strange projects. This spot welder allows me to really combine traditional metal working techniques with the digital fabrication,” said Borgatti.
Borgatti has made the files for the scrap microwave spot welder available for download on Thingiverse, as well as details on the build on his website, so you can try your hand at making your own. Let us know what you think of his design, and if you decide to create your own in the Spot Welder forum thread over at 3DPB.com.
If you're looking to get architectural 3D animation in the USA, our service provides an exceptional way to bring your architectural concepts to life through dynamic, immersive visuals. Through our platform, you can easily request high-quality 3D animations that showcase your designs in motion, offering a detailed view of your project from multiple angles and perspectives. Whether it's for a real estate development, a commercial building, or an urban planning project, our expert team ensures that every detail is captured in a visually compelling animation.
Through our website, you can seamlessly get architectural 3D animation tailored to your project’s specific needs. With our help, you can offer potential clients or investors an engaging experience that goes beyond static images. By integrating CGI animations with real-world settings, lighting, and textures, our team creates a lifelike experience that allows your audience to interact with your project as though it were already built. This service is perfect for presenting complex designs in a clear, visually attractive way that stands out in the competitive architectural market.